基于沸腾传热的热交换器和热沉被广泛应用于高热流密度产品表面的冷却散热。然而,随着高功率电子技术的快速发展,以及数据中心、集成电路、绝缘栅极双极晶体管(IGBTS)和新能源汽车等对器件表面高效冷却的需求,对狭窄空间高效冷却技术提出了严峻挑战。为了应对这些挑战,当前研究者已经提出了各种表面处理方法,以增强固液界面处的沸腾传热性能。已有的大量研究证明,在铜表面加工微通道结构是增强沸腾传热的有效方法,减小微通道结构间距以增大传热表面积,能够进一步提高沸腾传热性能。然而,由于缺乏低成本高效率的加工技术,微通道结构间距很难降至10 μm以内。此外,金属表面热功能微结构的深宽比与其应用性能如强化沸腾传热性能成正比,因此具有高深宽比特征的金属表面微结构在强化沸腾传热等重要工程领域中具有广阔的应用前景。金属微结构表面强化沸腾传热是复杂的科学问题与工程技术问题,本文研究的重点在于验证椭圆振动铲削加工的铜金属表面高深宽比微结构,应用于强化沸腾传热的有效性。
近期,清华大学机械工程系的李志伟博士,冯平法教授,张建富教授,郁鼎文教授,丁培员博士生,吴凯悦博士生和王健健副教授(通讯作者),在传热领域TOP期刊Applied Thermal Engineering上发表《Highly efficient boiling heat transfer of copper surface with sub-10 micron channels fabricated by elliptical vibration chiseling》的研究论文。本研究采用一种新颖的加工方法-椭圆振动铲削,在纯铜表面制备独特均匀的亚10 μm微通道结构,并研究了它们在增强沸腾传热方面的性能。铲削微结构的间距范围为1至10 μm,高度约为8 μm,深宽比在2至9之间。进一步在池沸腾传热实验平台上开展实验,以评估铲削表面的沸腾传热性能。实验结果表明,铲削的亚10 μm微通道结构可以极大地提高沸腾传热性能,尤其是传热系数(Heat Transfer Coefficient, HTC)的增强。与平面(未加工表面)相比,临界热流密度(Critical Heat Flux, CHF)和临界传热系数(HTC@CHF)分别提高了4%~49.5%和115%~195.8%。表面积增加是这些亚10 μm铜表面微通道结构沸腾传热性能增强的主要原因,表面积增加与HTC@CHF提升幅度成正比。本研究填补了铜表面亚10 μm微通道结构传热性能的空白,未来有望应用于各种小型传热冷却器件。
研究内容
- 微通道结构加工
首先使用椭圆振动铲削加工方法,在纯铜表面制备独特均匀的亚10 μm微通道结构,并研究它们在增强沸腾传热方面的性能。图1是椭圆振动铲削加工原理和实验样块示意图。实验样块加工表面即实验表面,直径为20 mm,加工表面与圆柱之间的台阶面为密封圈安装位置。台阶面的直径为24 mm。圆柱高20 mm,表面均匀分布的三个小孔自下而上形成了温度梯度。小孔之间的间距为5 mm,直径为2 mm。底座为长方体,用以安装陶瓷加热片以提供稳定热流。底座的大小为40 mm×40 mm×32 mm,边缘位置的四个通孔为表面微结构加工和强化沸腾传热实验的固定安装孔,直径均为3.5 mm。为保证实验表面高深宽比微结构加工的均一性,需要根据切削宽度严格控制相邻加工道次的间距即交叉进给。

图1 样品制备示意图,包括(a)椭圆振动铲削原理,(b)样块加工示意图和(c)实验样块尺寸。在多个实验样块表面制备具有不同间距的微通道结构,如图2所示。VCF5指微通道结构间距为5 μm,VCF7指微通道结构间距为7 μm,VCF10指微通道结构间距为10 μm。光滑实验样块表面平整无微结构,高低起伏范围为0-0.387 μm。VCF5实验样块表面分布有高深宽比微结构,高低起伏范围较大为0-20 μm,与SEM图对比,三维形貌结果能够大致反映出表面实际情况。而针对VCF10实验样块表面的三维形貌结果能够很好的反映出高深宽比微结构的实际情况,原因在于VCF10实验样块表面微结构的结构间距较大,光斑能够进入间隙中。VCF10实验样块表面的高低起伏范围也为0-20 μm。进一步统计实验样块表面微结构的三维形貌参数。其中,铲削微结构表面的高度h与结构间距Vc/f成正比,宽度w和深宽比与结构间距成反比,VCF3实验样块表面微结构的深宽比最大为8.74,VCF5、VCF7和VCF10实验样块表面微结构的深宽比分别为5.14、2.88和2.14。而EVC复合表面实验样块表面微结构的高度最小且宽度最大,深宽比最小为0.11,具有典型的低深宽比特征,将其作为低深宽比微结构表面的对照组。同时,制备了复合表面结构,如图3所示。

图2 不同加工参数下,实验样块表面的SEM形貌结果,包括(a)平面,(b)VCF5,(c)VCF10。
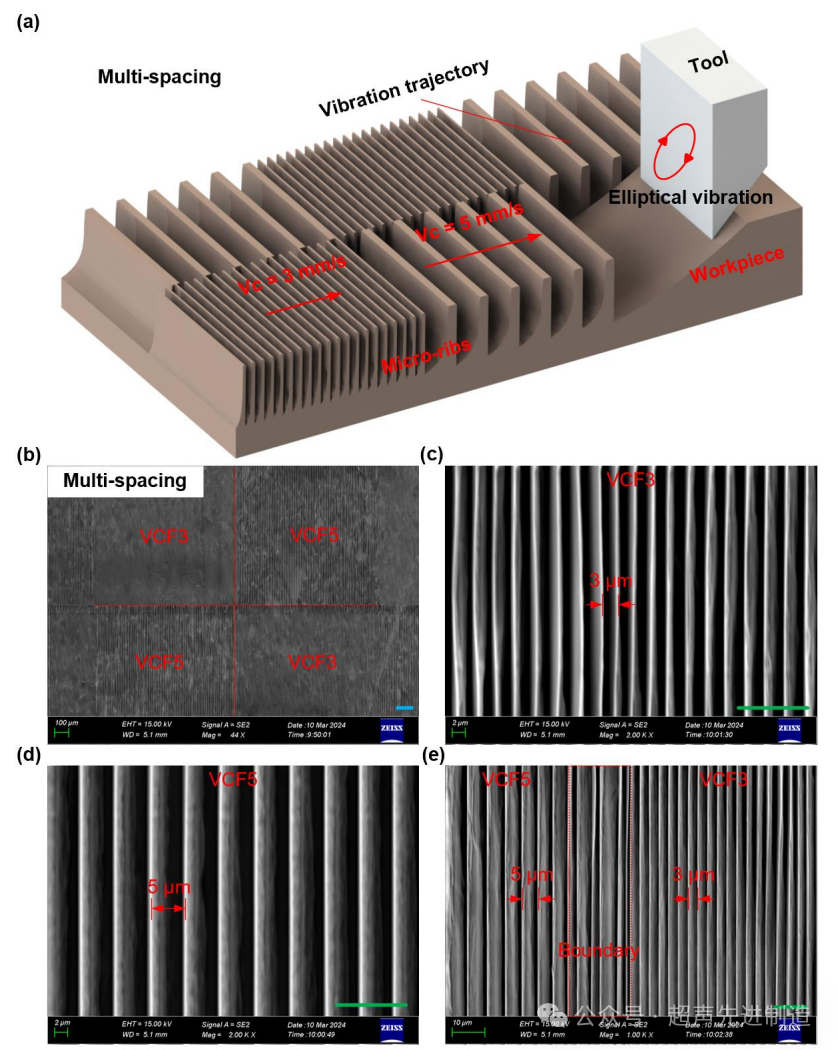
图3 复合表面结构制造方法及结果。
- 池沸腾实验平台搭建
综合考虑实验需求,设计沸腾传热实验台如图4所示。绘制各部件图纸并加工装配,搭建实际池沸腾实验平台。平台整体放置在独立空间中,室温维持在26 ℃左右。平台安装在实验框架内部,直流光源与高速摄像机对称放置,冷水机处于实验箱体下方,实验箱体安装在实验框架中层的不锈钢板上,加热维持系统和温度采集系统位于实验框架后侧。实验前,通过加热器循环加热去离子水,充分排出水中溶解气体。实验过程中,实验箱体中去离子水体积需要控制,一方面加热器需完全浸没在去离子水中,另一方面冷凝器需要远离水面。同时,随着样块表面热流密度的逐渐增加,汽泡逐渐产生,原位观测系统与温度采集系统连续记录数据。
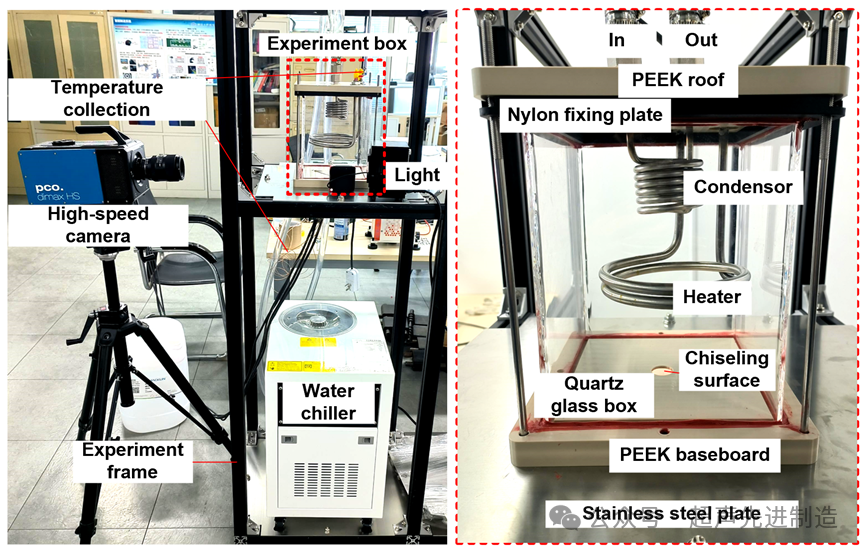
图4 沸腾传热实验台实物。
- 沸腾传热实验结果
使用沸腾传热实验台,针对不同实验样块开展实验,结果如图5所示。铲削表面的沸腾传热曲线在光滑表面的左上方,相同过热度下,铲削表面的热流密度更高,沸腾换热极限更高。铲削表面的传热系数曲线在光滑表面的正上方,相同热流密度下,铲削表面的传热系数更大,沸腾换热效率更高。在沸腾换热曲线和传热系数曲线中,所有曲线均在临界热流密度(CHF)处截至。
进一步根据重复实验结果,统计实验表面参数的平均值,结论如下:
1、铲削表面的ΔT@CHF远小于光滑表面,光滑表面的ΔT@CHF最大,VCF3的ΔT@CHF最小。随着结构间距的增加,铲削表面的ΔT@CHF逐渐增加。并且,铲削表面的ΔT@CHF的波动明显小于光滑表面。
2、所有铲削表面的CHF都高于光滑表面。随着结构间距的增加,铲削表面的CHF先增加后减少,VCF5具有最高的CHF,为152.49 W/cm²。光滑表面的CHF最小,为101.79 W/cm²。铲削表面的CHF最大提高了49.5%。
3、相比光滑表面,铲削表面的HTC@CHF提升非常明显。随着结构间距的增加,铲削表面的HTC@CHF逐渐降低。其中,VCF3具有最高的HTC@CHF,为10.5 W/cm²·K。光滑表面的HTC@CHF最低,为3.55 W/cm²·K。铲削表面的HTC@CHF最大提高了195.8%。结合铲削表面的深宽比测量结果,发现HTC@CHF与深宽比成正比。
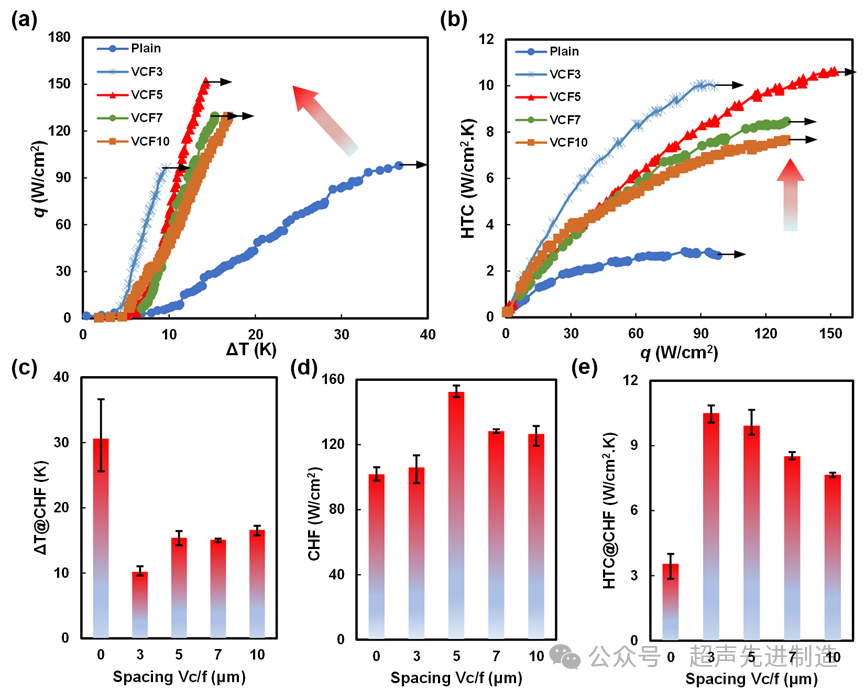

图5 沸腾传热实验结果及性能比较。
全文小结
本文将椭圆振动铲削加工的铜金属表面高深宽比微结构应用于强化沸腾传热,实现了其强化沸腾传热性能的大幅提升,并阐明了椭圆振动铲削加工技术的应用优势。椭圆振动铲削加工技术为铜金属表面高深宽比微结构在强化沸腾传热领域的应用,提供了新的先进加工技术支撑。主要研究内容和结论如下:
1、搭建了池沸腾实验平台以开展强化沸腾传热实验。设计加工了实验样块,并在实验样块表面实现了铜金属表面大规模高深宽比微结构的有效制备。池沸腾实验平台的设计合理可靠,热流密度的不确定度在4.9%以内,换热系数的不确定度在10.9%以内,能够应用于强化沸腾传热实验中;
2、获得了椭圆振动铲削铜金属高深宽比微结构表面的强化沸腾传热实际性能。其中,铲削表面的CHF最大达到了152.49 W/cm²,相比光滑表面提高了49.5%;HTC@CHF最大达到了10.5 W/cm²·K,相比光滑表面提高了195.8%。与已有文献中使用其他方法加工的金属微通道结构表面的强化沸腾传热性能进行对比,铲削表面的结构间距小,HTC@CHF提升幅度大。椭圆振动铲削加工技术具有加工尺度小和所加工微结构强化沸腾传热效率高的应用优势;
3、研究了汽泡生成特性、微结构比表面积和润湿性对强化沸腾传热性能的影响规律。实验样块表面的汽泡分离直径与其强化沸腾传热性能成正比,但汽泡分离频率与其强化沸腾传热性能无明显关系。比表面积提升与HTC@CHF提升成正比,但对CHF的影响不明显。各向异性的椭圆振动铲削微结构表面具有疏水性,影响了CHF的提升,并使其沸腾换热实验曲线单调上升;
4、提出了复合铲削微结构表面包括阵列表面和多级表面的制备方法,并针对所有复合微结构表面开展了沸腾强化传热实验。阵列表面和多级表面的比表面积远大于EVC复合表面,其对应的HTC@CHF也大于EVC复合表面,验证了比表面积提升对HTC@CHF提升的影响规律。此外,阵列表面的比表面积提升幅度介于VCF3和VCF5之间,其HTC@CHF结果也介于VCF3和VCF5之间。
论文信息
Li Z, Feng P, Zhang J, et al. Highly Efficient Boiling Heat Transfer of Copper Surface with Sub-10 Micron Channels Fabricated by Elliptical Vibration Chiseling[J]. Available at SSRN 4986642.